Zonder (flink wat) warmte kom je in de chemische industrie niet. Nu fabrieken afscheid moeten nemen van aardgas als warmtebron, wordt er volop gewerkt aan nieuwe warmtepompen die de benodigde hoge temperaturen kunnen leveren. Maar er zijn nog heel wat obstakels te overwinnen.
‘Het doel van de Nederlandse industrie is om in 2050 volledig duurzaam te zijn’, vertelt John Nijenhuis, senior technology manager bij de TU Delft. ‘Dit gaat op veel vlakken de goede kant op, maar warmte is nog wel een belangrijk obstakel.’ In chemische fabrieken is het beheersen van warmte van essentieel belang. Je moet warmte creëren die zorgt dat reacties verlopen, of juist warmte hergebruiken om verspilling te voorkomen.
’Voor industriële processen kun je niet zomaar een standaardsysteem uitrollen’
Simon Spoelstra
Deze ontwikkelingen gaan hard, maar ondertussen zijn veel fabrieken nog steeds afhankelijk van aardgas voor het produceren van warmte. Om ook daar een verduurzamingsslag te maken zijn nieuwe technieken nodig. Het probleem daarbij is vooral de diversiteit aan fabrieken en processen, zegt senior projectmanager Simon Spoelstra van TNO: ‘Voor woonhuizen kun je een paar standaard warmtesystemen overal toepassen. Industriële processen zijn allemaal anders, dus daar kun je niet zomaar een standaardsysteem uitrollen.’
Werkmedium
Een van de veelgenoemde opties is een hogetemperatuurwarmtepomp. ‘We hebben nu redelijk standaard warmtepompen die tot negentig graden kunnen verwarmen, zegt Spoelstra. ‘Maar voor industriële processen moeten we de temperatuur nog hoger krijgen.’ Het principe van een warmtepomp voor hoge temperaturen is niet wezenlijk anders dan een warmtepomp die een huis verwarmt. In beide gevallen gebruik je een zogenoemd werkmedium dat al bij lage temperatuur verdampt. In een woonhuis levert de buitenlucht de warmte voor het verdampen, in de industrie is dit restwarmte uit het proces. Het werkmedium verdampt en de damp wordt in een compressor op druk gebracht, waardoor de temperatuur stijgt. In een condensor geeft het gas de warmte weer af aan het warmtedistributiesysteem, en het condenseert terug naar een vloeistof.
Voor industriële warmtepompen gaat het echter om complexere processen als je hogere temperaturen wilt bereiken. Het verschil zit vooral in het werkmedium en de schaalgrootte, vertelt Spoelstra: ‘Het werkmedium moet worden afgestemd op de temperatuurcondities van de toepassing. De prestatie van de warmtepomp hangt vooral af van het temperatuurverschil tussen de warmtebron en de benodigde warmte. Hoe meer warmte er in de verdamper terecht komt, hoe meer warmte je uiteindelijk kunt afgeven.’
‘Een proces als Haber-Bosch zal niet snel op 200 graden lukken’
John Nijenhuis
De kunst is dus een werkmedium of een mengsel van werkmedia te vinden dat zo goed mogelijk past bij de toepassing. Spoelstra: ‘Vroeger deden we dit met chloorfluorkoolstofverbindingen en hun opvolgers, maar veel van deze middelen zijn binnenkort waarschijnlijk niet meer toegestaan. Wij gebruiken daarom koolwaterstoffen zoals butaan en pentaan.’ Hiermee is het al gelukt om 150 °C te bereiken, maar er zitten ook nadelen aan. ‘Deze gassen zijn natuurlijk enorm brandbaar, dus je moet wel heel zeker weten dat je je systeem veilig maakt.’
Heatflex
Ook Nijenhuis en zijn collega’s werken aan technologieën voor de industriële warmtehuishouding. Dit doen ze in het Heatflex-programma, een samenwerking tussen verschillende universiteiten, bedrijven en kennisinstellingen. ‘We willen weten hoe we fabrieken zo efficiënt mogelijk kunnen verwarmen zonder aardgas’, zegt Nijenhuis. ‘Hiervoor werken we samen met energiebedrijven zoals Eneco, bedrijven die warmtepompen en compressoren maken en heel veel fabrieken die bereid zijn nieuwe soorten warmtepompen en andere technieken in de praktijk te testen.’
Naast nieuwe werkmedia kijken ze bijvoorbeeld ook naar het ontwikkelen van efficiëntere compressoren voor industriële warmtepompen, zegt Rene Pecnik, hoogleraar energietechnologie aan de TU Delft: ‘Bijvoorbeeld compressoren die stoom gebruiken en zo misschien wel 250 graden kunnen halen.’ En ook het formaat van de warmtepomp is een aandachtspunt, zegt zijn collega Jurriaan Peeters, universitair hoofddocent energietechnologie. ‘We moeten kijken naar compactere systemen die makkelijk in een fabriek passen.’
‘We moeten kijken naar compactere systemen die makkelijk in een fabriek passen’
Jurriaan Peeters
Hierbij komt soms hulp uit onverwachte hoek. Zo vonden ze een bedrijf dat airconditioning voor vliegtuigen maakt en daarvoor heel efficiënte en kleine compressoren kan bouwen. Peeters: ‘Dit bedrijf is nu gekoppeld aan een bedrijf dat verpakkingsmateriaal maakt met behulp van een droogproces en daarbij veel warmte nodig heeft. Zij zijn nu samen bezig om een kleine, efficiënte warmtepomp te bouwen die ook geïntegreerd kan worden in productieprocessen.’ Het zou ook helpen als dit soort systemen meteen worden meegenomen in het ontwerp van de fabriek. Pecnik: ‘Maar omdat fabrieken zo lang meegaan, moeten we in de tussentijd ook flexibelere oplossingen vinden.’
Prijzig
Een serieus obstakel bij dit soort projecten is de grote investering. ‘Er wordt heel veel op maat gemaakt, en dat maakt het prijzig’, zegt Spoelstra. En wat ook nog meespeelt: met 200 °C ben je nog lang niet op het niveau dat veel processen nodig hebben. ‘We moeten nog hoger, en daarvoor is nog veel ontwikkeling nodig’, zegt Pecnik. ‘Nieuwe media en compressoren, maar misschien ook wel nieuwe soorten warmtepompen zoals thermo-akoestische systemen.’ Daarbij verwachten de onderzoekers overigens dat de procestemperaturen nog gaan zakken. ‘Uit duurzaamheidsoogpunt kijken veel fabrieken ook of ze op lagere temperaturen kunnen opereren, dat zou mooi samengaan.’
’Misschien moeten we naar nieuwe soorten warmtepompen zoals thermo-akoestische systemen’
René Pecnik
Natuurlijk is dat niet altijd mogelijk. ‘Een proces als Haber-Bosch zal niet snel op tweehonderd graden lukken’, zegt Nijenhuis. Daarom kijken de onderzoekers ook naar het direct elektrisch verwarmen van reactoren, als een soort elektrische pan. ‘Dit is wel mogelijk, maar het kost een hoop extra elektriciteit’, zegt Spoelstra. Sowieso vormt die balans een puzzel. ‘Nu is twintig procent van de energievraag van een fabriek elektriciteit, als dat meer wordt moet het elektriciteitsnet het wel aankunnen.’ Bovendien is er (nog) geen continu aanbod van duurzame elektriciteit. Daarom kijken de Heatflex onderzoekers ook naar mogelijkheden om warmte op te slaan en zo de fluctuaties op te vangen. Daar zijn op zich nu al oplossingen voor, maar er is een schaalvergroting nodig, zegt Peeters: ‘Zo kun je warmte bijvoorbeeld opslaan in materialen die van fase veranderen zoals gesmolten zouten, of in reagerende materialen.’
Genoeg ideeën en opties dus, nu is het volgens Nijenhuis vooral een kwestie van uitzoeken wat werkt. ‘We weten van veel ideeën nog niet hoe het werkt, of maar half. Dus we moeten nog veel kennis opdoen.’ De tijd begint wel een beetje te dringen, want in 2035 willen de onderzoekers al concrete resultaten hebben. ‘Dan willen we alle pilots zo goed als afgerond hebben en fabrieken een duidelijk overzicht kunnen geven van wat werkt, zodat ze kunnen gaan implementeren.’
Spoelstra ziet dat de verschuiving steeds sneller gaat: ‘Er werken steeds meer mensen aan dit probleem. Niet alleen in onderzoek, ook bijvoorbeeld in het standaardiseren van de productie van warmtepompen. Dat helpt ook enorm in het maken van stappen. En we moeten ook wel, als we in 2050 een nieuwe industrie willen.’
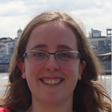
Nog geen opmerkingen