Ook een goed idee verkoopt zichzelf niet, weten ze bij BioBTX. Hun goede idee: plastic afval omzetten in ‘groene’ aromaten die zo weer richting de industrie kunnen als drop-in chemical. Maar er was flink wat inzet en tijd nodig om de financiering van een eerste plant op commerciële schaal rond had. ‘Je moet echt de tijd nemen om te zorgen dat iedereen elkaar begrijpt.’
Het was groot nieuws toen afgelopen juni het Groningse BioBTX bekendmaakte dat ze een investering van €80 miljoen hadden binnengehengeld om een fabriek te bouwen op het chemiepark Delfzijl. Niet zomaar een fabriek, maar een heuse first-of-a-kind installatie om op commercieel relevante schaal ‘groene’ aromaten te produceren. Via de door BioBTX ontwikkelde ICCP-technologie, integrated cascaded catalytic pyrolysis, wordt plastic afval in twee stappen omgezet in BTX; benzeen, tolueen, xyleen. Deze veelgebruikte aromaten zijn vervolgens geschikt als drop-in chemical in uiteenlopende, gangbare productieprocessen in de chemische industrie.
Afvalplastic wordt hiermee een waardevolle grondstof voor bouwstenen die nu nog uit fossiele feedstocks worden gehaald. Nadat ze zich bij BioBTX 2,5 jaar lang de blaren op de tong hebben gepraat om het geld los te krijgen, is het nu eindelijk tijd voor de ultieme stap: een volwaardige fabriek uit de grond stampen die eind 2026 20 kton plastic afval per jaar omzet.
Nu de eerste euforie na deze financiële klapper een beetje is gezakt, kijken we met BioBTX ceo Ton Vries en extern adviseur Peter Nieuwenhuizen terug naar het financieringstraject. Hoe hebben ze dit aangepakt, wat bleken grote obstakels, waren er ook meevallers en, vooral, welke lessen heeft dit opgeleverd?
‘We wilden meteen de stap maken naar een plant die zichzelf kan bedruipen’
Ton Vries
Maar eerst even een korte historische schets. In de jaren 2011-2012 lukte het een team van chemici van de Rijksuniversiteit Groningen en het eveneens Groningse Syncom, waar Ton Vries destijds de scepter zwaaide, om uit houtachtige biomassa een mix van benzeen, tolueen en xyleen (BTX) te produceren. Gaandeweg werd de focus verlegd naar plastic als grondstof en ook dat lukte. ‘We konden dus aromaten maken uit die alternatieve feedstocks en dan ga je denken over de volgende stap naar grotere volumes’, zegt Vries. ‘We hebben toen, zo’n vijf jaar geleden, een pilot plant gebouwd waar we 10 tot 20 kilogram per uur konden verwerken. Dat was overigens ook al een aardige investering, want dat kost je toch vijf tot zes ton. Maar het werkte goed.’
Kostendekkend
Tijd voor weer een volgende stap, maar dat moest in de ogen van het BioBTX-team dan ook het echte werk zijn. Geen tussenfases en probeersels meer. Vries: ‘We wilden meteen de stap maken naar een plant die zichzelf kan bedruipen en daarmee bedoel ik dat je genoeg produceert om de operationele kosten zoals personeel en elektriciteit etc., te dekken. Dus dachten we aan een capaciteit van 50 kiloton, maar dat bleek toch wel erg prijzig.’ Nou zou je misschien denken dat het nogal voor de hand ligt om, als je naar een commercieel haalbare fabriek wilt, zo’n nieuwe plant in ieder geval kostendekkend te laten zijn. ‘Ja, dat lijkt heel logisch, maar in de praktijk gebeurt het nauwelijks’, legt Peter Nieuwenhuizen uit. Hij heeft vanuit zijn industriële ervaring bij AkzoNobel/Nouryon en daarna als investeerder en fondsmanager regelmatig gezien dat het daarop juist stuk loopt. ‘Wat je vaak ziet is dat partijen voor een te kleine pilot gaan, waardoor er continu geld bij moet om de boel draaiende te houden. Ieder jaar moeten er miljoenen naartoe, maar het levert niks op. En dan wordt zo’n pilot plant een blok aan het been.’
‘Je ziet vaak dat partijen voor een te kleine pilot plant gaan’
Peter Nieuwenhuizen
Dus les 1: ga in een keer voor de grote klap. Maar hoe groot moet die dan zijn? ‘We zijn flink gaan rekenen en 20 kton leek de ideale omvang’, aldus Vries. ‘Dat volume is groot genoeg om quitte te draaien, groot genoeg om de haalbaarheid te demonstreren en tegelijkertijd nog behapbaar qua initiële investeringen.’ Het oorspronkelijke doel van 50 kton is overigens niet helemaal van de baan. ‘Dat hebben we wel in het achterhoofd gehouden bij de keuze van de locatie, zodat uitbreiding naar die schaal daar alsnog kan.’
Toch klinkt 20 kton niet als een omvang waarmee je meespeelt in de megatonnenliga van de conventionele bulkindustrie. In de “nieuwe” chemische industrie die op heel andere feedstocks draait zijn de volumes ook anders dan we zijn gewend, aldus Nieuwenhuizen. ‘Met olie als feedstock kun je naar duizenden kilotonnen, maar als je andere uitgangstoffen gebruikt moet je rekening houden met de afstand tot de fabriek. In ons geval gaat het om plastic afval of andere reststromen en die moeten per vrachtwagen worden aangevoerd. Dat loont tot een bepaalde afstand. Als die vrachtwagens van verder moeten komen, kun je beter daar ook een fabriek bouwen.’ Die 20 kton is niet zomaar uit de lucht komen vallen, zegt Vries. ‘Je ziet voor dit nieuwe type feedstocks dat de plants zich bewegen tussen de 20 en 200 kton. En ook 20 kton betekent nog steeds een flinke opschaling. Van onze pilot van 10 kg per uur naar ruim 2000 kg per uur is toch factor 200. Dat is een flinke engineering klus. Gelukkig is daar in Nederland veel financiering voor, bijvoorbeeld via de RVO [Rijksdienst voor Ondernemend Nederland, red.] kun je conceptual design financieren. Dan praat je al snel over €500.000.’
Externe expertise
Het brengt ons bij een tweede lesson learned die Vries graag deelt. ‘Je kunt er bijna niet genoeg engineering power opzetten, je bouwt dat natuurlijk op, maar uiteindelijk zit je zo op 20 man.’ En we rollen naadloos door naar les nummer 3, want zodra je aan het engineeren slaat, moet je ook het vergunningstraject in gang zetten. ‘Dat hele proces neemt gemakkelijk drie tot vier jaar in beslag en, heel belangrijk, huur hier externe expertise voor in. Wij hebben dit traject met Royal Haskoning gedaan en ja, het inhuren van een bureau betekent ook meteen dat je kosten maakt, maar zonder een partij met verstand van zaken red je het niet. Je moet dit gewoon meteen goed aanpakken.’
‘Je kunt er bijna niet genoeg engineering power opzetten’
Ton Vries
Wijze lessen, maar als je eenmaal aan de vergunningen begint, leg je jezelf dan niet teveel vast met betrekking tot het ontwerp? Hoeveel ruimte heb je nog om gaandeweg je engineering bij te sturen? ‘Daar zit inderdaad een optimum in’, zegt Nieuwenhuizen. ‘Er komt daarom ook een bepaalde entrepreneursmentaliteit bij kijken, en Ton heeft die, om op een gegeven te durven zeggen “We weten nog niet alles, maar we weten wel genoeg voor deze stap”, want anders kom je er niet. Daarom is het ook zo belangrijk op een ervaren partij erbij te betrekken die weet hoe deze processen lopen zodat je op de juiste manier aan het traject begint.’ Hier zit echter ook wel een les in voor de chemieclusters en bedrijvenparken, vindt Vries. ‘Het zou echt heel fijn zijn als er vanuit de chemieclusters meer coördinatie zou zijn, want bij de bouw van een plant komen veel zaken overeen en nu moet iedereen het allemaal zelf weer opnieuw doen. Daar is volgens mij nog echt wel iets te winnen.’
Gaandeweg het ontwerpen en uitwerken en parallel daaraan het vergunningentraject komen de totale kosten van de nieuwe plant steeds beter in beeld. Toen dat kostenplaatje eenmaal helder was, begon het spel pas echt. Zeker omdat ze besloten niet voor de gangbare stapsgewijze aanpak te gaan. Vries: ‘Wij hebben ervoor gekozen om in een klap het geld voor de fabriek bij elkaar te krijgen.’ Een gedurfde stap, want dat betekende een overgang van subsidies en aandeelhoudersbijdragen in de ordegrootte van tonnen meteen naar een som van tientallen miljoenen. Bij wie moet je dan aankloppen? ‘Voor dit type investeringen zijn er verschillende bronnen’, zegt Nieuwenhuizen. ‘Er zijn subsidies vanuit bijvoobeeld Economische Zaken, je hebt een partij als InvestNL die meefinanciert, er zijn de echte financiële partijen die puur voor het rendement gaan en dan zijn er partijen die je als “strategisch” kunt beschouwen. Denk aan andere bedrijven voor wie dit een mooie kans is om meteen vooraan te zitten. Dat kunnen grote namen zijn die nu al aromaten produceren, dat kunnen gebruikers van aromaten zijn zoals in ons geval Covestro die als investeerder is ingestapt en het kunnen ook bedrijven zijn die de bouw interessant vinden en daar kansen zien. Al met al hebben we met zo’n 20 partijen gepraat.’
Een (langdurig) spel
Veel gepraat en lang gepraat. Vries en Nieuwenhuizen zijn 2,5 jaar continu in gesprek geweest met alles en iedereen. Want hoewel iedere partij toch over relevante expertise en ervaring beschikt, vinden ze elkaar niet vanzelf. Nieuwenhuizen: ‘Wij waren echt nodig om te zorgen dat iedereen, dus de strategisch geïnteresseerde bedrijven, de financiële partijen en de overheidsorganisaties elkaar daadwerkelijk goed begrepen. Daar moet je echt goed de tijd voor nemen.’ Voor Vries zit hier ook weer een belangrijke les in: ‘In dit hele spel is het belangrijk dat je inhoudelijk de taal spreekt.’
‘Al met al hebben we met zo’n 20 partijen gepraat’
Peter Nieuwenhuizen
Maar het was ook zeker een spel, vult Nieuwenhuizen aan. ‘Je bent steeds bezig om de een over de streep te trekken door erop te wijzen wat een ander (mogelijk) gaat doen. Het grote voordeel in ons geval was dat we al concreet iets in handen hebben. We hebben een product waar ook al een duidelijke markt met afnemers voor is. Dit kan echt een klapper worden. Daar moet je ook mee spelen.’ Nieuwenhuizen glundert hier iets meer bij dan Vries voor wie het wel echt als een heel lange tijd voelde. ‘Maar als we het stap voor stap hadden gedaan, met kleine mijlpalen, en steeds weer een beetje geld erbij, zou het nog langer duren voor je echt die fabriek hebt’, zegt Nieuwenhuizen. ‘En bovendien moet je dan steeds weer je engineering aanpassen, want gaandeweg verandert er altijd wel iets.’
Door wel voor de volle mep in een keer te gaan kunnen ze nu veel doelgerichter en efficiënter aan de slag, aldus Vries. ‘Dat we het geld hebben geeft ook vertrouwen bij de bouwers en andere partijen dat het echt gaat gebeuren. We kunnen meteen op volle kracht van start.’ Op naar eind 2026, want dan moet de nieuwe fabriek operationeel zijn. ‘Het eerste resultaat hadden we in 2011, nu zijn we 13 jaar verder en hebben we het geld en dan nog twee jaar voordat we een serieuze fabriek hebben’, verzucht Vries. ‘ De chemie is, net als de farma, echt een wereld van de lange adem.’ Nog een les die steeds weer wordt geleerd.
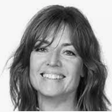
Nog geen opmerkingen