Met een investering van €80 miljoen op zak gaat BioBTX in Delfzijl een grootschalige fabriek bouwen voor de productie van benzeen, tolueen en xyleen uit afvalplastics. Dankzij een door het bedrijf ontwikkeld tweestapsproces kunnen deze basischemicaliën met hoge yield worden geproduceerd uit een breed scala aan grondstoffen.
Op 20 december 2012, in de laboratoria van de Rijksuniversiteit Groningen, produceerde start-up BioBTX haar eerste batch benzeen, tolueen en xyleen (BTX) uit houtachtige biomassa. Dankzij de door hen ontwikkelde integrated cascading catalytic pyrolysis (ICCP)-technologie wisten ze deze belangrijke bouwstenen voor de chemische industrie te produceren. Het zou de basis blijken voor de commerciële fabriek die het bedrijf nu in Delfzijl gaat bouwen.
De door BioBTX ontwikkelde iccp-technologie bestaat uit twee geïntegreerde processtappen. In de eerste stap worden de grondstoffen gepyrolyseerd, in de tweede stap vindt de katalytische upgrading plaats. Deze tweestapsbenadering zorgt voor een grote flexibiliteit voor wat betreft de grondstoffen, vertelt Niels Schenk, chief technology officer van BioBTX en mede-bedenker van het ICCP-proces. ‘Het proces is erg flexibel aan de inputkant. Door de grondstoffen te pyrolyseren, komen de organische stoffen in dampvorm en kunnen naar de upgrader worden geleid om vloeibare aromaten te produceren. Mineralen en andere reststoffen blijven achter.’
Thermodynamisch voordelig
Benzeen, tolueen en xyleen zijn drie belangrijke bouwstenen voor de chemische industrie. ‘Dat is ook de reden waarom we ervoor gekozen hebben om juist BTX te produceren. We kunnen daarmee enorme impact hebben. De volumes zijn groot en de moleculen zijn eenvoudig. Deze basischemicaliën hebben een hoge waarde’, aldus Schenk. De interesse vanuit de markt voor groene aromaten als “drop in” chemical neemt volgens hem toe. ‘Dat is ook de reden dat Covestro onlangs is ingestapt als investeerder en aandeelhouder.’ Daarbij zijn aromaten thermodynamisch erg stabiel. ‘Koolstofatomen vormen graag aromaatverbindingen, omdat dit thermodynamisch voordelig is. En onze katalysator, een zeoliet, vormt graag aromaten.’
Bij de oprichting startte het bedrijf met houtachtige biomassa als grondstof. ‘Een nadeel hiervan is dat er veel cokes worden gevormd bij pyrolyse van hout. We hebben in de eerste pilotinstallatie veel verschillende grondstoffen getest’, zegt Schenk. Glycerine was één van de opties. ‘Glycerine is een bijproduct van de biodieselproductie. Dat was een product met een lage waarde. Maar de prijs van glycerine steeg omdat het steeds minder op de markt kwam. Het werd namelijk ook als cosubstraat in mestvergisting gebruikt. Daarvoor was toentertijd subsidie beschikbaar, terwijl voor dat niet zo was voor het gebruik van glycerine als grondstof voor chemicaliën’. De prijs was echter niet de enige reden om niet door te gaan met glycerine. ‘De helft van de massa van glycerine is zuurstof. Om BTX te produceren, moet de zuurstof uit het proces worden gehaald. Dat gebeurt in de vorm van CO, CO2 en water. Dat betekent dat je ook koolstof uit het proces haalt. De opbrengst zal daarom nooit boven de vijftig procent uitkomen.’
[Lees verder onder de foto]
Mixed waste
Mede-ingegeven door de Europese wetgeving en ambities om meer afvalplastics te recyclen stapte BioBTX zo’n vijf jaar geleden over op deze stroom als grondstof. ‘Pyrolyse van polyolefines levert een theoretische yield van honderd procent. We kunnen nu gemengde afvalplastics en afvalolie met ons proces omzetten in BTX’, vertelt Schenk. Dankzij een recente succesvolle investeringsronde van meer dan €80 miljoen, kan de innovatieve onderneming nu haar technologie opschalen en in Delfzijl een fabriek bouwen. In eerste instantie krijgt de installatie een capaciteit om 20.000 ton plastic afval per jaar te verwerken. In een tweede fase wordt dit opgeschaald naar 50.000 ton. Schenk: ‘In Delfzijl bouwen we in de eerste fase een unit die geschikt is voor de verwerking van gemengde afvalplastics. Maar op het terrein is nog ruimte beschikbaar, daar kunnen we ook een unit plaatsen voor de verwerking van biomassa als grondstof.’
Maar voordat er kon worden nagedacht over opschalen, heeft het BioBTX het proces juist gedownscaled. ‘We hadden een pilotinstallatie staan die voor bepaalde grondstoffen was geoptimaliseerd. Door deze terug te brengen naar een kleinere schaal konden we meer flexibiliteit aanbrengen in het proces en in de grondstoffen. Hierdoor hebben we de BTX-opbrengst verhoogd.’ Opschalen was vervolgens hard werken om het proces draaiende te krijgen, zegt Schenk met een veelbetekenende glimlach. ‘Toen we startten met het gebruik van mixed waste plastics als grondstof, stopte de pilotinstallatie steeds na vijftien minuten. Dan moest je hem open maken, het probleem zoeken en oplossen en weer opstarten. Je komt dingen tegen die je van tevoren niet kunt voorzien. Daaruit hebben we veel geleerd over de procescondities en de katalysator. Die informatie gebruiken we nu voor de engineering van de commerciële fabriek.’
De verwachting is dat de nieuwe installatie eind 2026 in gebruik wordt genomen. ‘Dit is voor ons echter niet het einddoel’, aldus Schenk. ‘De fabriek wordt een “first of a kind”, een showcase om de technologie in licentie te verkopen.’
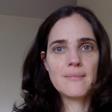
Nog geen opmerkingen