Simple molecules can be used to make a biodegradable glue that is stronger than current petroleum-based mass products. And it does not have to be much more expensive, write US researchers in Science.
Eugene Chen (Colorado State University) and colleagues use beta-butyrolactone (BBL), which can be made by reacting propylene oxide with carbon monoxide. BBL in turn polymerises into poly(3-hydroxybutyrate), or P3HB for short. Some microorganisms are known to produce this naturally as a backup food source. But attempts to do something useful with it on an industrial scale have not been very successful: the stuff was too brittle.
This seems to be because there are two stereoisomers of BBL. In the polymerisation reaction, the CH3 side groups can end up at either side of the chain. If they are all on the same side, it is called a syndiotactic polymer. Alternating sides are called isotactic, and in an atactic polymer they are randomly distributed. The latter is amorphous; the first two are regular enough to easily form crystals.
A microorganism probably synthesises them enzymatically in a particular form, because it doesn’t need to stick. But for really good glue you need a mixed form, says Groningen professor Marleen Kamperman. Her group has done a lot of research in recent years on “natural” high-strength polymers, such as mussel glue and spider silk. “Small, hard crystalline pieces in an amorphous matrix make these materials strong and ductile. They have the right balance between elastic and viscous behaviour. Something that is too elastic cannot dissipate energy properly, making the material less tough. And a material that is too viscous starts to flow too quickly and is therefore not resistant to creep.’
P3HB library
Chen’s group developed a method to systematically test this. They synthesised a kind of cyclic dimerisation of BBL, i.e. with two stereocentres whose position could be adjusted. By playing with ten different organic homogeneous catalysts, they then created a library of P3HB variants, each with a specific stereochemical structure that could be predicted quite accurately. What they came up with should come as no surprise, given the above. Purely atactic, syndiotactic or isotactic P3HB is useless as an adhesive. But a mixture in which the chains are 42 to 66 per cent syndiotactic works all the better. Possibly even better than the researchers’ expectations. Kamperman points out that it is impossible to tell from the publication how much of this was deliberate - it could just have been luck.
They then worked empirically with the optimal recipe, comparing it with, for example, ‘Gorilla Glue’, a polyurethane-based product from the US. They also made samples of it for a hot-melt glue gun, which normally uses heated EVA, a copolymer of ethylene and vinyl acetate that is used to glue cardboard boxes, for example. The partially syndiotactic P3HB was often found to produce stronger bonds than the commercial products you buy in the supermarket, whether with cardboard, wood, glass, aluminium or steel. Even when (or perhaps because?) the surface to be bonded was only superficially polished beforehand.
[article continues below the image]
The authors claim this is partly because the amorphous-crystalline blend follows the rough substrate better. ‘But this has not been proven’, argues Kamperman. ‘It also seems to be very difficult to measure in practice and is not the most important factor in making a strong adhesive.’ However, she sees another important detail in the results: ‘You can see that the adhesive gets stronger at higher strains. We call this strain hardening, a very important property for really good adhesives.’
Scaling up?
In fact, using Aspen Plus process simulation software, the authors have already done a preliminary design of a factory that could produce this adhesive. It turns out that it does not even need to be much more expensive than conventional EVA cartridges. If biodegradability is added to the equation, it should be commercially viable.
Note that the calculation is based on petroleum-based propylene oxide. It is technically possible to make it from renewable resources, but the costs of large-scale production are not yet sufficiently clear. The same applies to homogeneous catalysts, which are rather exotic and currently only available in laboratory quantities. On the other hand, the advantage is that only two variants are needed, one to make BBL and one to polymerise it - once the desired composition is known, cyclic dimerisation as an intermediate step is in principle no longer necessary.
Zhen Zhang, Ethan Quinn, et al, Stereomicrostructure-regulated biodegradable adhesives, Science (2025), doi: 10.1126/science.adr7175
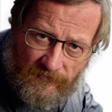
Nog geen opmerkingen